As with any kind of plastic repair or craft, selecting an adhesive determines whether the bond is durable or a source of frustration. On the market today, Gorilla Glue and Super Glue are two of the most well-known options, each famous for their strength and versatility. However, all adhesives differ, and these two options will prove useful for different kinds of plastic. In this article, we will discuss both Super Glue and Gorilla Glue, depending on their characteristics, benefits, and limitations, in order to provide a thorough comparison to assist you in choosing the right one for your project. Whether you need to repair a household item, work on a DIY project, or have a more specialized requirement, this guide will give you the knowledge to make a confident decision.
What is the Difference Between Gorilla Glue and Super Glue for Plastic?
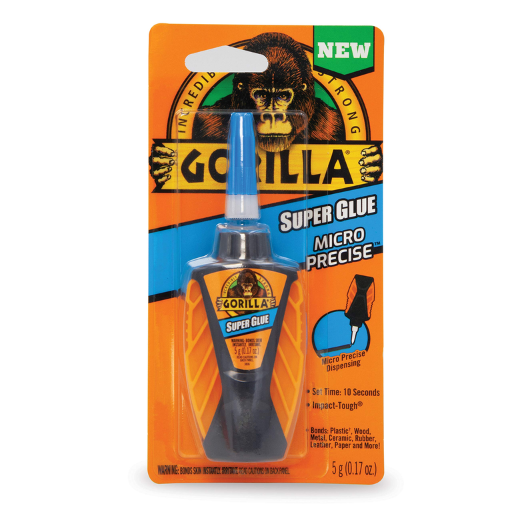
What sets Gorilla Glue and Super Glue apart is both their composition and their bonding techniques with plastics. Gorilla Glue two-part adhesive expands while curing which helps fill irregular surfaces. Polyurethane based glues work best when exposed to moisture, They do not work with some plastic types especially with PE and PP plastics.
Super Glue is the direct opposite of the gorilla brand glue. Unlike super glue that works best for porous or rough surfaced plastics, super glue is not affected by a spray of water. It is a type of glue that falls under cyanoacrylate adhesives, and it seals fast while forming a firm and hard bond. It works best for smooth less porous plastic surfaces because it does not expand while curing. One major difference between the two super glue has is that it can be stressed easily. It works quickly but provides less relief than gorilla glue which is A lot more flexible after curing. It is important to note that the type of adhesive to be used to a plastic pended on the kind of plastic and the bonding requirements.
How Does Gorilla Glue Work on Plastic Surfaces?
Gorilla Glue works on the surfaces of plastics due to its moisture-activating polyurethane based chemistry. The glue expands while curing, strengthening the bond. Because of this it is very useful for plastic surfaces that are porous or uneven where other adhesives would not work. Still, some kinds of plastics like polyethylene and polypropylene pose problems because of surface energy. Surface treatment such as sanding or primer application is suggested for those materials. Due to exposure to temperatures and moisture even years later, joined surfaces will shift and weak places will appear. Projects that need long-lasting results and are sensitive to environmental factors like humidity and temperature changes are best served by Gorilla Glue.
Is Super Glue Suitable for All Types of Plastic?
Super glue, also referred to as cyanoacrylate adhesive, serves as a powerful bonding agent for many types of plastics. Has a polystyrene (PS), polyvinyl chloride (PVC), and ABS super glue works extremely well due to their chemical bonding. However, it fails to work with lower grade adhesive plastics like polyethylene (PE) and polypropylene (PP) which have an adhesive bond resistance. To assist adhesion activation on these materials, low energy surfaces like roughening the surface abrasion or applying a plastic primer are strongly recommended. Also, super glues formulated for plastic bonding usually contain some activators for better adhesive performance emphasizing how critical adhesive selection is based on the tough plastic material.
What are the Key Ingredients in Gorilla Super Glue and Super Glue?
Key Ingredient |
Gorilla Super Glue |
Super Glue |
---|---|---|
Cyanoacrylate Compound |
Yes, main ingredient |
Yes, primary adhesive component |
Rubber Particles |
Yes, for added impact resistance |
No |
Water-Resistant Formula |
Yes, resists moisture and humidity |
No, less resistant to water |
Bonding Time |
10-45 seconds |
10-30 seconds |
Heat Resistance |
Moderate |
Low |
Surface Compatibility |
Broad range, includes some plastics |
Limited, not ideal for all plastics |
Flexibility |
Enhanced for soft impacts |
Brittle after curing |
Shelf Life |
Longer with proper storage |
Shorter than Gorilla Super Glue |
Filler Requirement |
Works without fillers |
Can require fillers for gaps |
Strength |
High, built for durability |
Moderate, less structural strength |
When Should You Use Gorilla Glue Versus Super Glue for Plastic Repairs?
Gorilla glue works best for repairing plastic where flexibility, strength, and bonding of wide variety of materials (including some uncommon plastics) is needed. It is great for things that are going to have light impacts, or things that need to be stored for a longer duration before use.
On the other hand, Super Glue functions best for prompt, small scale repairs needing instant adhesion. It is effective on smooth surfaces, but plastic parts that need to be flexible or strong supersede soft core bond, do not pliable gaps will best strong supplementary gaps won’t perform properly.
What Types of Plastic are Best Suited for Gorilla Glue?
Gorilla Glue is very flexible and bonds well with many types of plastics, especially those that are porous or have a roughened surface. It can be used on polyethylene terephthalate (PET), acrylonitrile butadiene styrene (ABS), and polycarbonate plastics as these materials have better structural properties and will bind stronger due to their composition. However, this does not mean that polyethylene (PE) or polypropylene (PP) non-porous plastics will be without challenges, as they also require surface treatments such as priming or sanding done so that the surface would begin to allow bond formation. Projects that deal with uneven surfaces require these strong adhesive qualities gorilla glue since during bond formation, the glue expanding allows firm bonding which makes it much easier for long lasting dependable projects and using the word tough on surfaces that deal with long lasting and strong consistent effectiveness.
When is Super Glue the Better Option for Repairing Plastic?
Also called super glue, cyanoacrylate adhesive is often the best option for repairing plastic parts under precision work, fast curing, and low expansion scenarios. Unlike Gorilla Glue, super glue, which will not distort the surface, rigidly bonds to the surface, making it perfect for small and intricate repairs or applications where dimensional stability is a must. More so, super glue forms strong bonds with non-porous plastics like polyethylene (PE) and polypropylene (PP) with the right primers made for those materials. Bonding takes only a few seconds which makes it convenient for instant repairs. Super glue is known to provide strong bonds in thin layers, giving it an edge over other expanding adhesives when used in plastic repair works where discreet and clean joints are crucial.
How to Properly Use Gorilla Glue and Super Glue on Plastic?
For both super glue and gorilla glue, the initial steps remain identical:
- Prepare the Surface
Firstly, cleaning the plastic surface to get rid of grease, dust, as well as any contaminants is vital. In addition, light sanding can be done on non-porous plastics to improve the bond.
- Apply the Glue
For super glue, moisture is not needed, so a thin layer spread on one side will suffice. Gorilla glue requires the other side to be slightly damp, after which, glue can be applied to the dry face.
- Join the Pieces
Both need the tilted surfaces joined within seconds, and application of pressure for a minimum of 15-60 seconds for super glue. Regaining full bond strength requires up to 2 hours of clamping for Gorilla Glue to cure fully.
- Allow Time to Cure
Super Glue has a maximum bond strength in 24 hours, which is much longer than the initial setting time. Gorilla Glue reaches its maximum efficacy after a full 24-hour cure time.
- Handle with Caution
Follow the guidance on the label and ensure your workspace provides sufficient airflow. They also recommend skin coverings to prevent contact with the glue that may lead to skin injuries.
How to Ensure a Strong Bond with Super Glue on Plastic?
- Surface Preparation
Followed by surface cleaning with isopropyl alcohol or soap and water, the remnants of dirt, grease, or residues are removed with care, performing surface cleaning. Ensuring deep precision with super glue on plastic requires the surfaces to be thoroughly wiped and dried, allowing a vastly smooth surface free from contamination. Lastly, for lightly roughened plastics such as polyethylene or polypropylene, super glue’s adhesion can be slightly improved by roughening the bonding area using some fine sandpaper between 120 and 200 grits. Ensuring the absence of dust after the step wipes away any residue formed during this final stage exposes a clean bond for gluing.
- Adhesive Application
Use super glue in moderation by applying a small dot to one of the surfaces you have prepared. Do not use excess super glue since it weakens the bond as well as extends curing times. Tighter bonding plastics may require either a cyanoacrylate adhesive made for plastics or a primer intended for plastics. Make sure the parts fit and fix them accurately while applying constant pressure for 30 to 60 seconds until a preliminary bond is set.
- Curing and Strengthening the Bond
Accurate alignment of the surfaces helps ensure an effective bond. Superglue tends to create a bond between surfaces at lightning speed but requires up to 24 hours to achieve optimum strength. During this time, IT is crucial to keep the bonded surfaces static in a controlled environment. Adding more durable elastic materials around the surfaces while curing can increase durability. Following the recommended guidelines helps increase overall enduring mechanical performance of the bonds.
What Precautions Should You Take When Using Super Glue?
Exercise proper safety measures, including eye and respiratory protective equipment, adds another layer of consideration. Work only in a space with sufficient airflow and ventilation to avoid potential health-damaging fumes. Direct breathing of cyanoacrylate vapors can irritate the respiratory and eye systems. Never put on protective hand gear for fungal infections because it will result in glue exposure through hand contact; super adhesive fuses with skin almost effortlessly and is hard to remove. In case of skin contact, do not try to forcefully separate the bonded skin; instead, soak the area in warm, soapy water to slowly dissolve the bond. Furthermore, children and pets should be kept away from super glues because a small sip can pose a big danger. Super glues should be preserved in low and dry conditions with no exposure to heat or flames because they are a fire hazard. Following these procedures allow the use of super glues effectively without risking safety.
Are There Any Specific Conditions for Using Gorilla Glue or Super Glue on Plastic?
Yes, there are conditions for the use of either super glue or gorilla glue on plastics. The gorilla glue works best for plastics that have a bit of a rough surface because the glue needs some voids to set. Clean and dry the surface before applying the glue and make sure there is no oil or dirt on the surface. Super glue works best for small plastic repairs and non porous plastic like polystyrene or acrylic works best.
Both types of glue may be ineffective on some plastic polyethylene (PE) or polypropylene (PP), which are non-stick surfaces that resist bonding. To enhance adhesion to these materials, a primer designed for plastics may be used. primers. These materials have to be paired with some form of adhesive, claiming compatibility with these plastics. Always follow the manufacturer’s recommendations for the best outcome.
What Environmental Factors Affect the Performance of Gorilla Glue?
Relay bonding of glue can be very crucial in areas such as its curing, strength bonding and even long term durability over the period of time. Here mentioned details are some of the critical factors to pay attention to:
- Temperature
Best bonding temperatures for gouila glue falls between 40°F (4°C) and 100°F (38°C). If temperatures drop below these range, bond strength may be weakened and curing may be slowed. On the other hand, if there is extreme high temperatures bonding speed may be increased but will risk the strength of the bond.
- Humidity
Gorilla glue uses water as part of its key ingredients, therefore requires water to be moisture activated. Decreased amounts of humidity can cause slow curing of adhesives. On the other side, environments with excessive humidity and foam may weaken the bond if not placed properly during application.
- Surface Moisture
To ensure activation of adhesive, surface moisture is vital. But excess moisture can dilute glue, thus affecting its efficiency. Performance of glue works best when proper balance is maintained.
- Exposure to UV Light
UV light exposure caused changes in bonds such as discoloration, weakening of structural integrity and others. Due to these issues, shielding bonded areas from exposing them to sunlight is recommended due to attached UV shields.
- Pressure and Weight During Curing
Applying appropriate clamping pressure during the curing stage can greatly improve the bond strength of Gorilla Glue. Nonetheless, environmental factors such as vibrations or weight bearing down during the adhesive curing process may impede adhesive setting and compromise final bond strength.
Does Humidity Impact the Effectiveness of Super Glue?
Of course, the comeback of moisture substantially affects the performance level of super glue owing to the latter’s need for dampness to kickstart the curing process. Glue cures, a super glue which is a cyanoacrylate adhesive, cures as a result of a chemical reaction caused by dampness either in the atmosphere or on the surfaces of the glue. Less moisture can lead to either the curing process taking longer than usual or the adhesive not curing completely which results in diminished bond strength. On the other hand, too much humidity can force the adhesive to cure way too fast which can cause extractable brittle-like defects or a significant drop in adhesion strength.
Can Gorilla Glue or Super Glue be Used on Different Types of Plastic?
Super glue and Gorilla glue are adhesives that can work on different kinds of plastics. However, their ability to perform is not always guaranteed. Super glue or cyanoacrylate, whose representative products are in rigid plastic form like polystyrene and acrylic, will perform better than PE and PP. These two make use of slippery surfaces and non-porous surfaces. These pink slippers do not try to perform in terms of water and instead of using a primer made for plastics. A gap does exist for the latter cases but not for smoother or oily surface, except some preparations and proper steps are taken. Always check the glue’s product specifications to ensure compatibility with the specific type of plastic you are working with.
Gorilla Glue on Polypropylene vs Polyethylene
Additional steps such as surface preparation via shredding can augment adhesive bonding. This is because increased area and texture allows for better adhesion of glue to the material. Alternatively, primers tailored for low energy plastics greatly enhance adhesion. Manufacturer supplied technical data suggests that the adhesive’s formulation does not adequately support bonds with flat, non-porous surfaces such as PP and PE, but bond formation is possible using some combination of preparation techniques. For such projects, specialty adhesives formulated for low energy materials are recommended to achieve the best structural strength.
Super Glue Applications on Various Plastic Types
Super glue, scientifically known as cyanoacrylate adhesive, showcases multifunctional bonding capabilities on a variety of plastic materials, albeit not all make suitable substrates. For super glue bond strengths to be useful in repairing household items, prototyping or low weight bearing applications, the plastic used should be rigid and over fifty percent of the polymers widely used today with rigid structures such as ABS (Acrylonitrile Butadiene Styrene). For lower rigid plastics like PVC (Polyvinyl Chloride), flexibility along with resistance to stress is dependent on surface preparation and correct adhesive choice.
Industries operating in demanding sectors have additional requirements for advanced engineering grade thermoplastics like polycarbonate or nylon that require chemical, thermal expansion, and heat resistance of the plastic to also be bonded to. It has been shown that surface treatments such as abrasion and priming increases bond strength because they increase surface energy and wettability. Of utmost importance, for very inert non reactive plastics such as polypropylene and polyethylene, strongly modified forms of cyanoacrylate containing primers or activators are needed to attain adequate adhesion so that it is applicable in the packaging, automotive, and medical fields where these materials are used in large quantities.
Reference Sources
- Original Gorilla Glue – Discusses the types of plastics Gorilla Glue works well on and its limitations.
- Best Glue For Plastic – Our Guide – Explains different types of glues for plastic, including Gorilla Glue.
- Can You Use Gorilla Glue On Plastic – Details the effectiveness of Gorilla Glue on various plastics.
- Super Glue 0.8 oz. Clear Sandable Plastic Glue/Epoxy – Highlights the features of Gorilla Super Glue for plastic repairs.
Frequently Asked Questions (FAQs)
Q: Which is glue safe for use on polypropylene plastic?
A: Gorilla super glue gel is recommended for use on polypropylene plastic, as it forms good bonds and is designed for long-lasting repairs.
Q: How does Gorilla Super Glue Gel compare to Krazy Glue?
A: Both Gorilla Super Glue Gel and Krazy Glue are cyanoacrylate glues, but Gorilla Super Glue Gel is thicker, allowing for better control and less excess glue during application.
Q: Can I use super glue on thick plastic?
A: Yes, super glue, including Gorilla Super Glue Gel, can be used on thick plastic, provided the surfaces are clean and properly prepared for a strong glue bond.
Q: How long does it take for Gorilla Super Glue Gel to dry?
A: Gorilla Super Glue Gel typically dries in 10 to 30 seconds, but full curing may take longer, depending on the amount applied and the type of surface glued.
Q: What should I do if I have excess glue on my project?
A: If you have excess glue, you can carefully remove it with a paper towel before it cures. Once cured, excess glue can be difficult to remove.
Q: Does Gorilla Super Glue gel work on polyethylene or polypropylene plastic?
A: Yes, gorilla super glue gel is effective on polyethylene or polypropylene plastic, as it is developed for long-lasting repairs on a variety of materials including plastics.
Q: Is using super glue necessary to protect my work area?
A: Yes, it is essential to protect your work area from spills when using super glue, as it can create a strong bond to unintended surfaces.
Q: How do I ensure a strong glue bond between two surfaces?
A: To ensure a strong glue bond, apply a small amount of Gorilla Super Glue Gel to one surface, press the two surfaces together firmly, and allow it to cure without movement.
Q: What type of glue is recommended for plastic bottles?
A: Gorilla super glue gel or other cyanoacrylate glues are recommended for plastic bottles, as they provide an airtight seal for maximum reusability.